Electric Motor
Posted by Tom Lee on
Introduction
This article will take an in-depth look at electric motors.
The article will bring more understanding on topics such as:
- Principle of Electric Motors
- Types of Electric Motors
- Applications and Benefits of Electric Motors
- And Much More…
Chapter 1: Principle of Electric Motors
This chapter will discuss what electric motors are, their construction, and how they function.
What is an Electric Motor?
An electric motor is an electric machine that converts electrical energy to mechanical energy. Most electric motors work via the interaction of the motor magnetic field and electrical current in a wound wire to produce force in the manner of torque supplied on the motor shaft. An electrical generator is identical mechanically to an electrical motor but functions with a reversed flow of energy, converting mechanical power to electrical power.

Electric motors may be driven by direct current (DC) supplies, like from rectifiers or batteries, or by alternating current (AC) supplies, like a power grid, electrical generators, or inverters. Electric motors can be categorized by concerns such as power supply type, application, construction, and type of movement output. They may be energized by DC or AC, be brushless or brushed, three-phase, two-phase, or single-phase, radial flux or axial, and can be liquid-cooled or air-cooled.
Standardized motors offer appropriate mechanical energy for industrial use. Applications include blowers and pumps, industrial fans, machine tools, power tools, household appliances, disk drives, and vehicles. Small motors can be found in electrical watches. In certain uses, like in regenerative braking in traction motors, electric motors may be utilized in reverse as generators that recover power that may otherwise be lost as friction and heat.
Construction of an Electric Motor
Two mechanical components of electric motors are the stator, which is fixed and the rotor, which moves. It also has two electrical components, magnets set and an armature, one of them is attached to the stator and the other to the rotor, together making a magnetic circuit.
Field magnets produce a magnetic field that passes through the winding. These may be permanent magnets or electromagnets. The field magnet is generally on the stator and the winding on the rotor, but in other motor types these are reversed.
Electric Motor Bearings
Bearings support the rotor and allow the rotor to spin on its axis. The motor housing in turn supports the bearings.
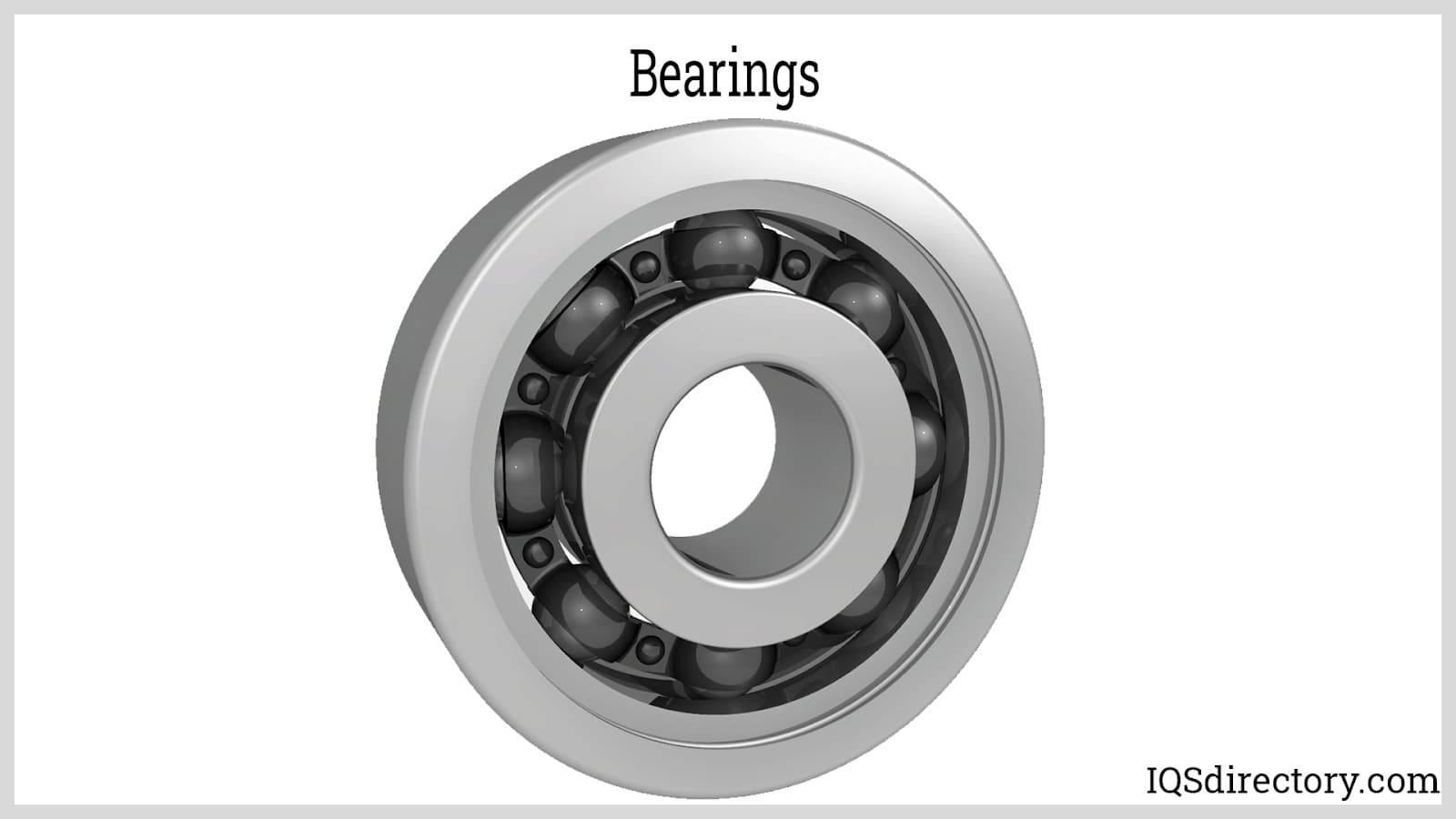
Electric Motor Rotor
The rotor is the mobile part that supplies the mechanical power. The rotor generally holds conductors which carry current and the stator magnetic field applies a force on to spin the shaft. Alternatively, other rotors have permanent magnets, and conductors are held by the stator. Permanent magnets give high efficiency over a bigger power range and working speed.
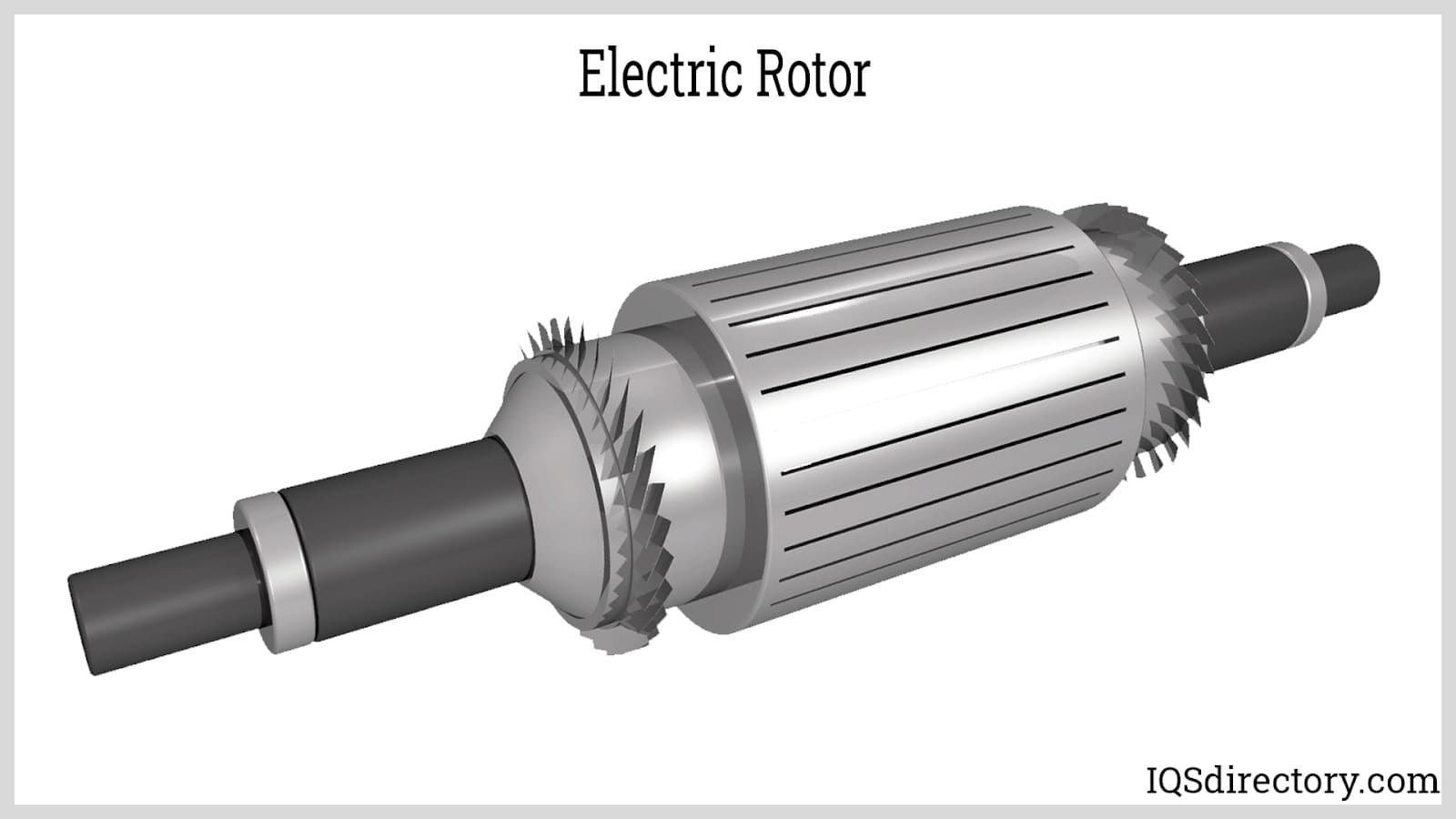
The air gap between the rotor and stator allows it to spin. The breadth of the gap has an important effect on the motor electrical properties. It is commonly made to be as small as possible, since a large gap produces weak performance. It is the primary source for the low power factor with which motors function. The energizing current rises and power factor reduces with the air gap, hence narrow gaps are better. Conversely, gaps which are very small may cause mechanical problems on top of losses and noise.
The motor shaft protrudes through bearings to the motor’s outer side, where the load is placed. Because the force of the load is applied beyond the furthest outer bearing, load is overhung.
Electric Motor Stator
The stator surrounds the rotor, and generally holds the field magnets, these are either electromagnets consisting of wound wire on a ferromagnetic core of iron or permanent magnets. These produce a magnetic field that passes through the rotor winding, applying force on the winding. The stator iron core is made of many thin metallic sheets which have insulation from each other, known as laminations.
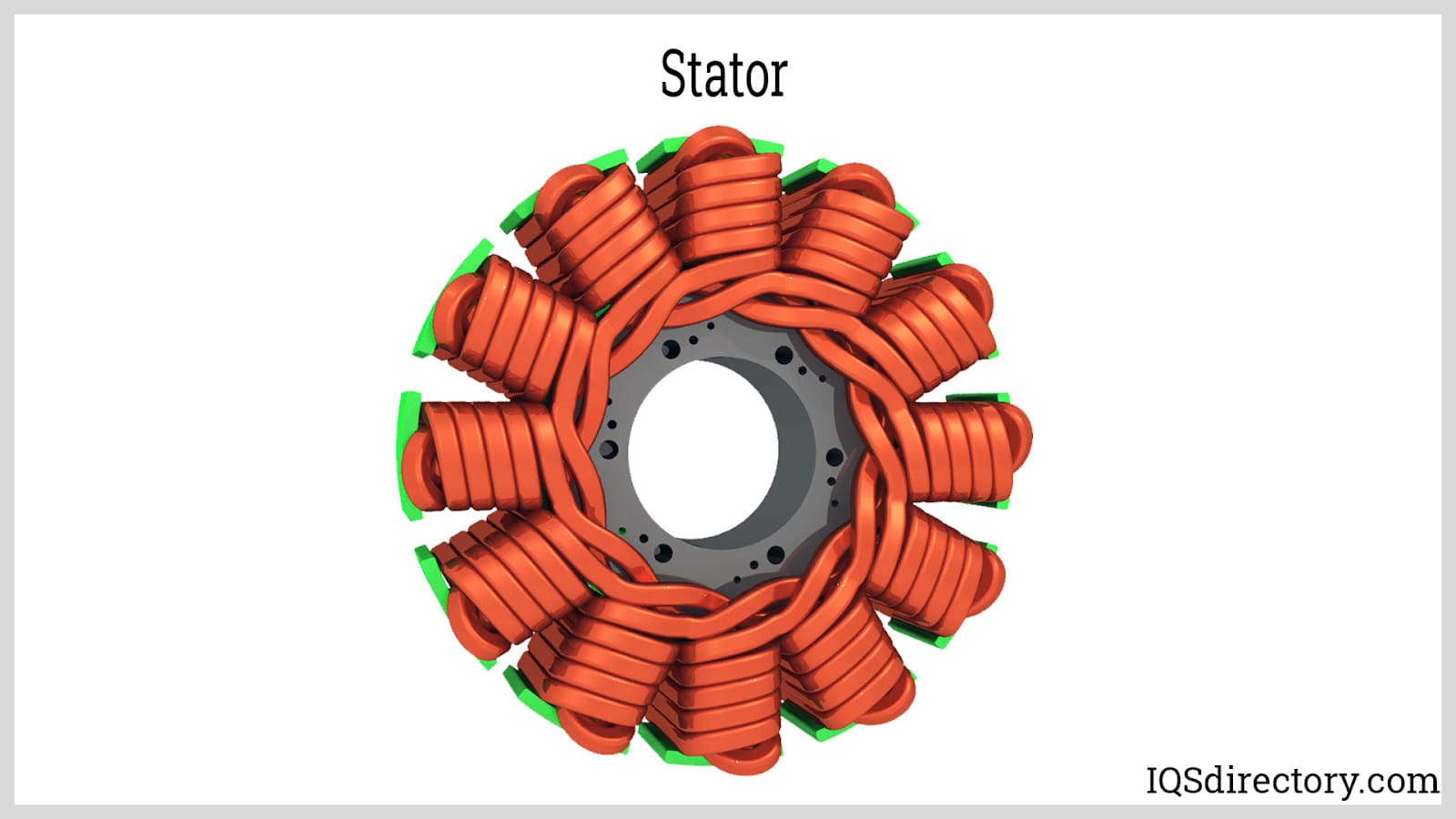
Lamination is utilized to lower energy loss which results if a solid core is utilized. Resin-packed motors, utilized in air conditioners and washing machines, utilize the damping attributes of plastic to lower vibration and noise.
Electric Motor Armature
The armature comprises wound wire on a ferromagnetic core. Current flowing through wire makes the magnetic field exert a Lorentz force onto it, rotating the rotor, which supplies the mechanical output. Windings are wires which are applied in coils, generally wrapped around a soft, laminated, iron, ferromagnetic core to produce magnetic poles when supplied with current.
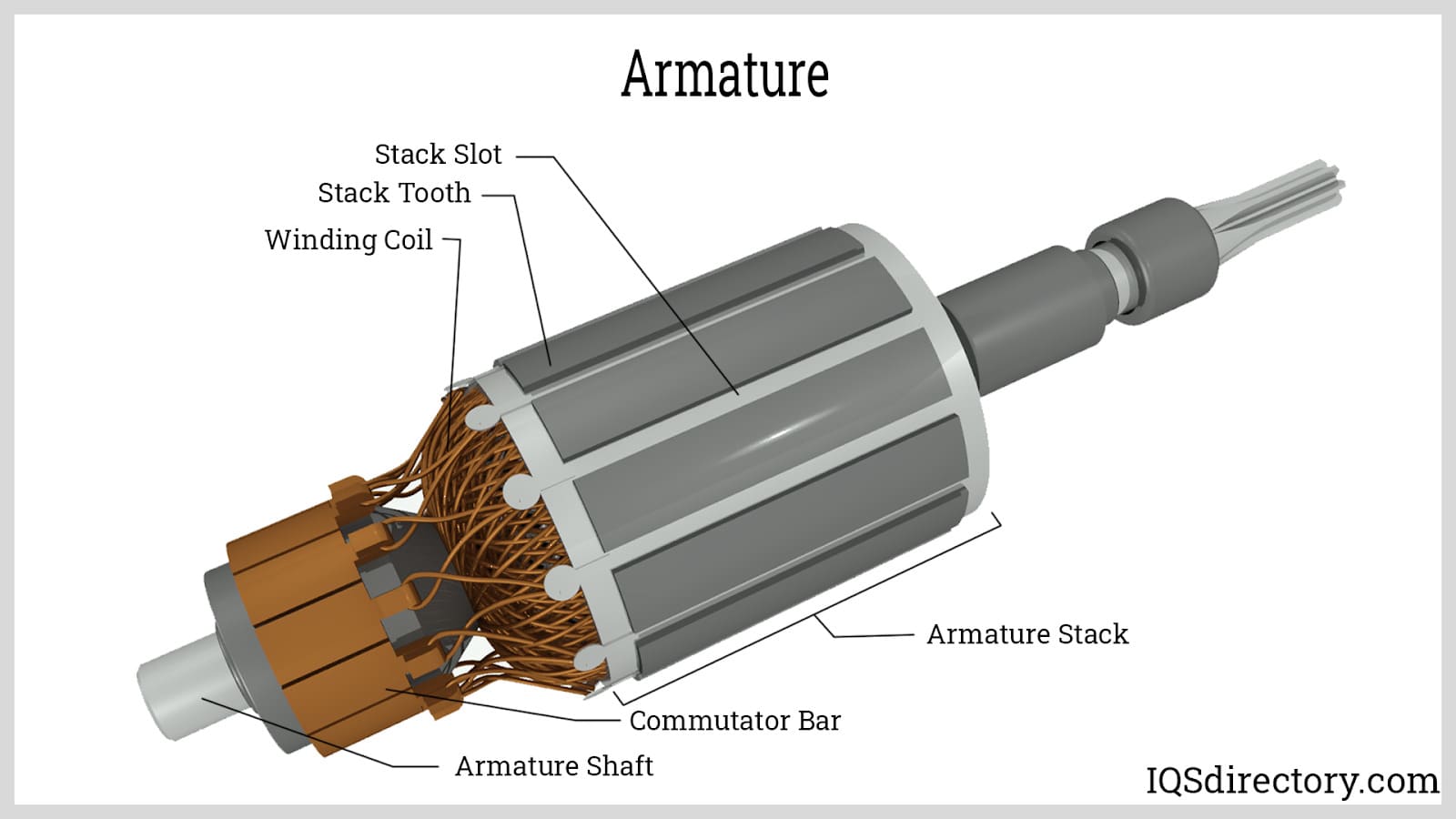
Electric motors come in non-salient and salient-pole setups. In salient-pole motors, the cores on the stator and rotor have projections known as poles facing one another, with a wound wire around every pole under the pole face, which becomes south or north poles of the field when current moves through the wire. In non-salient-pole (or round-rotor or distributed field) motors, the core is a cylinder, with the wound wire distributed equally in slots around the circumference. Supplying AC current in the windings generates poles in the ferromagnetic core which spin continuously. Shaded-pole motors have windings around a part of the pole, which delays the magnetic field phase for that pole.
Electric Motor Commutator
A commutator is a rotary electric switch which supplies alternating or direct current to the rotor. It periodically reverses the current flow in the rotor winding as the shaft spins. It comprises a cylinder made of multiple metal contact sections on the armature. Electrical contacts named "brushes" consisted of a soft conductor material like carbon pressed onto the commutator. The brushes create sliding contacts with consecutive commutator sections as it spins, offering current onto the rotor.
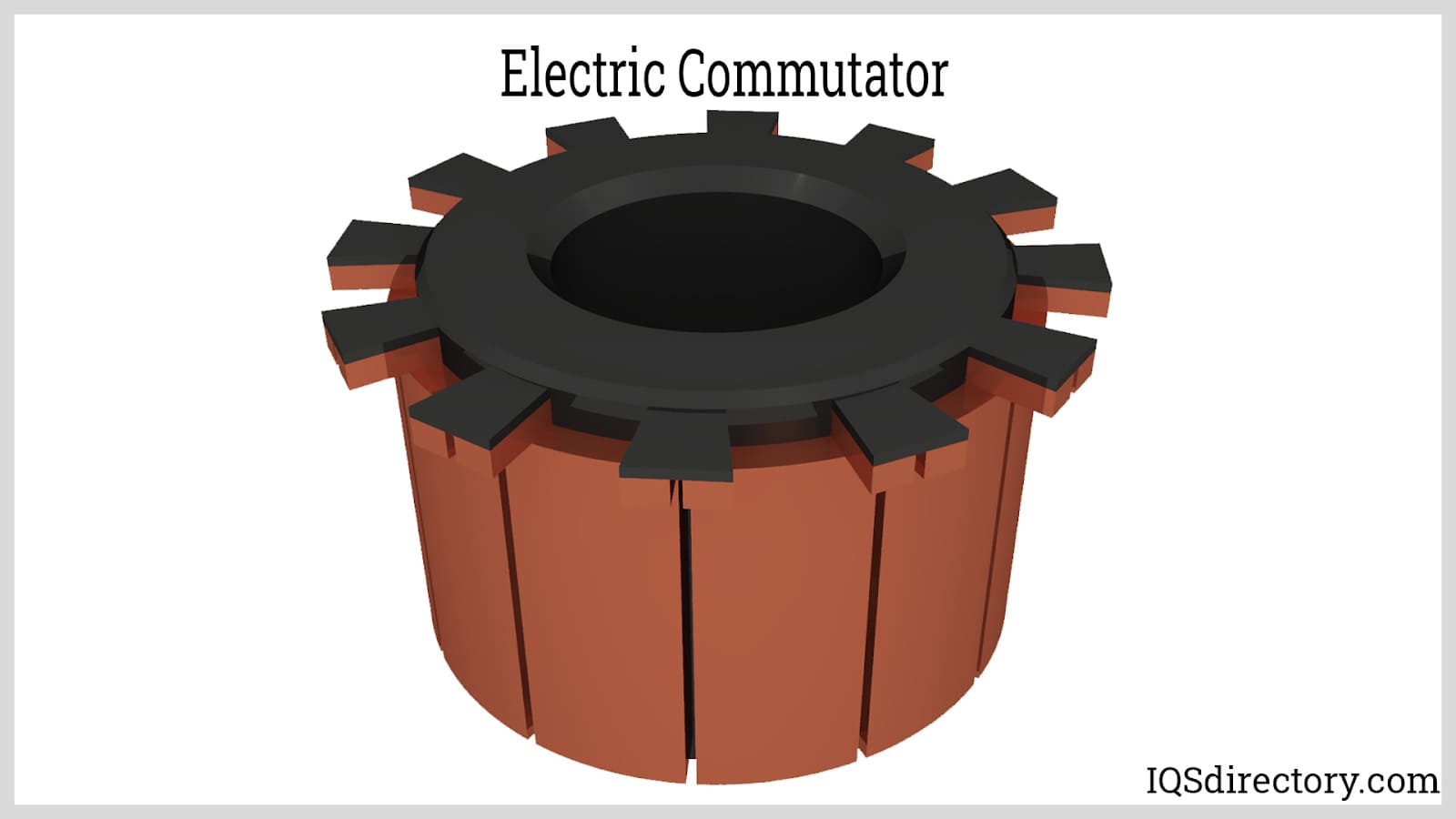
The rotor wire wounds are connected to the commutator sections. The commutator reverses the direction of current periodically in the rotor windings with each a half turn (180°), hence torque exerted to the rotor is in the same direction always. Without this current reversal, the torque direction on every winding of the rotor would reverse on each half a turn, hence the rotor stops. Commutators are incompetent and commutator motors have been frequently replaced by brushless DC motors, induction motors and permanent magnet motors.
How an Electric Motor Functions
Electric motors function by changing electrical power (AC or DC) to mechanical power in order to produce motion. Force is created within a motor via the interaction between winding direct (DC) or alternating (AC) current and a magnetic field. As the current flow strength rises, so does the magnetic field strength. With Ohm's law (V = R*I) in mind, voltage should rise so as to maintain constant current as resistance rises.
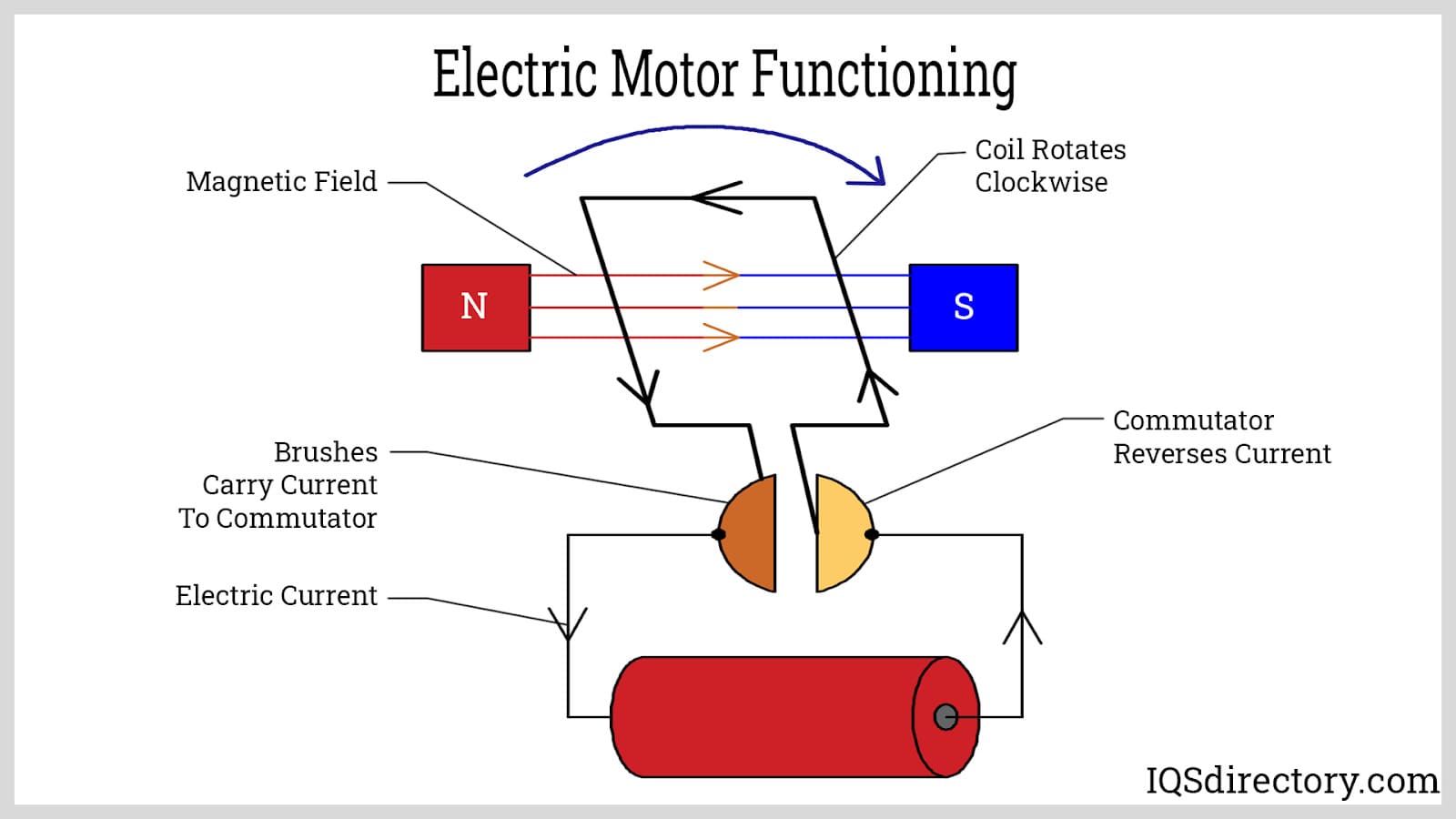
Considerations When Choosing Electric Motors
The considerations when choosing electric motors include:
Voltage – Is there access to a wall socket or is there a need for a product that can run on batteries. If a wall socket is available, the voltage standard could be 230VAC or more for industrial use.
Frequency – Motors operate at 60Hz for products working within the United States, but if a product will be utilized outside of the United States, there is a need to consider a 50Hz option. Speed – Is there a speed range at which the motor must operate. If adjustable or exact speeds are imminent, there may be a need to improve control to the motor.
Torque – How much starting torque is needed for an application? Does the torque needed from the motor change throughout the motor’s period of function? The worst case scenario torque amount of an application must be considered.
Power – When offering specifications, it should be known if the motor will be running on maximum power.
Duty Cycle – It is pertinent to know a motor's duty cycle. If the application will be running continuously such that the motor reaches full operating temperature or in short spans for the motor to cool down completely between cycles. Motors that run discontinuously can sometimes use small motors with the same torque and speed, but run continuously.
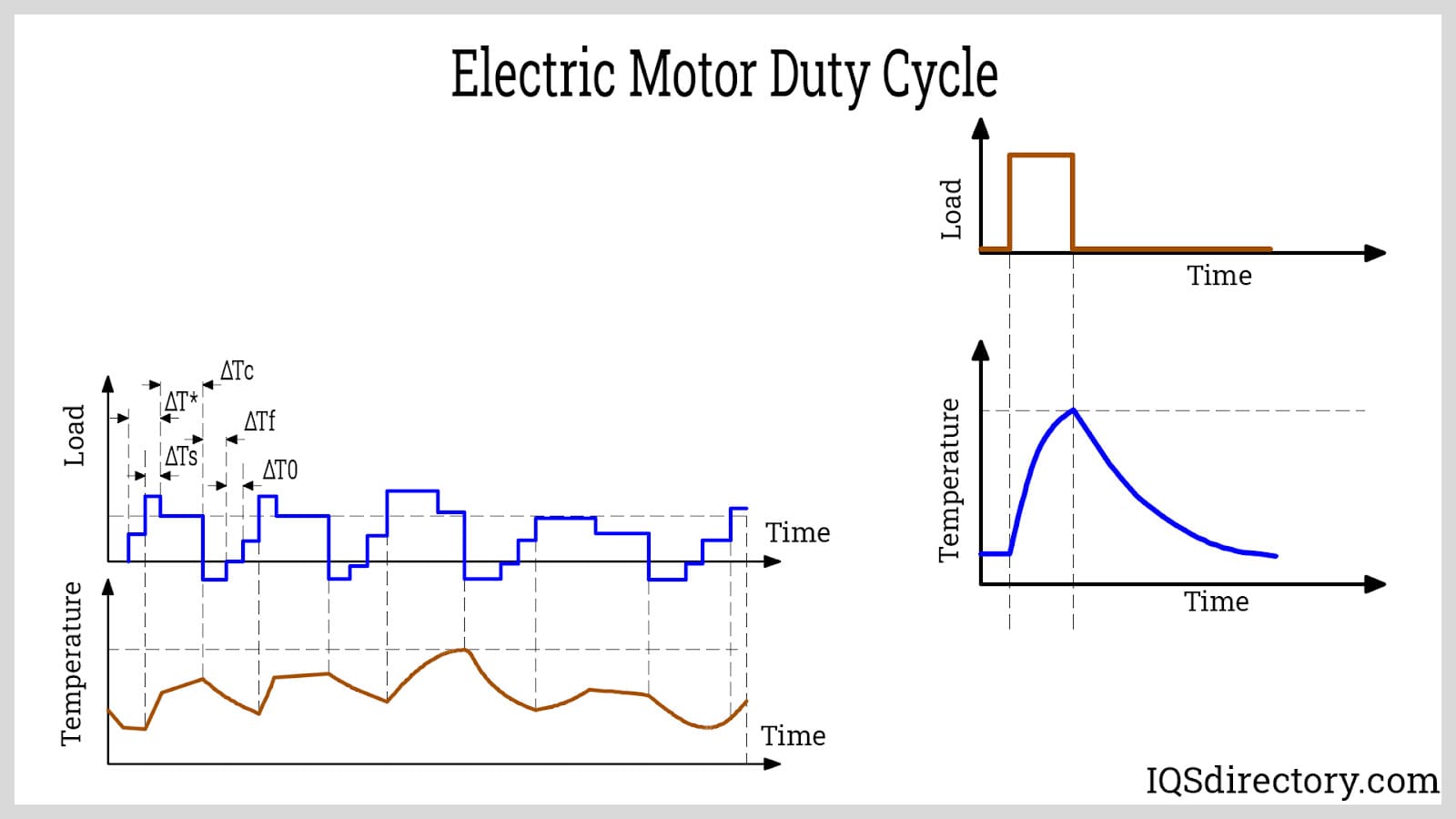
Life Cycle – Applications that operate very discontinuously can at times get on with a short life cycle and high maintenance needs of Universal and DC motors. Applications that operate continuously and need to function for numerous hours without maintenance may need a brushless DC or an AC motor with a very long lifespan.
Chapter 2: Types of Electric Motors
The different types of electric motors include:
DC Motors
A DC motor is any motor of a type of rotary electrical machine which converts electrical energy from direct current (DC) into mechanical energy. The most general types depend on the force created by magnetic fields. Almost all kinds of DC motors have some internal operation, either electronic or electromechanical, to change the current direction periodically in a part of the motor.
DC motors were the first kind of motor commonly utilized, as they can be powered from present direct current lighting energy distributing systems. DC motor speed may be controlled over a broad range, utilizing either a variable voltage supply or by altering the current strength in its field winding. Small DC motors are applied in appliances, toys, and tools. The universal DC motor can work on direct current but it is a light brushed motor utilized for portable appliances and power tools. Large DC motors are presently utilized in the propulsion of elevators and hoists, electric vehicles, and in drives for rolling mills for steel. With the arrival of power electronics replacement of DC motors with AC motors has been made conceivable in many applications.
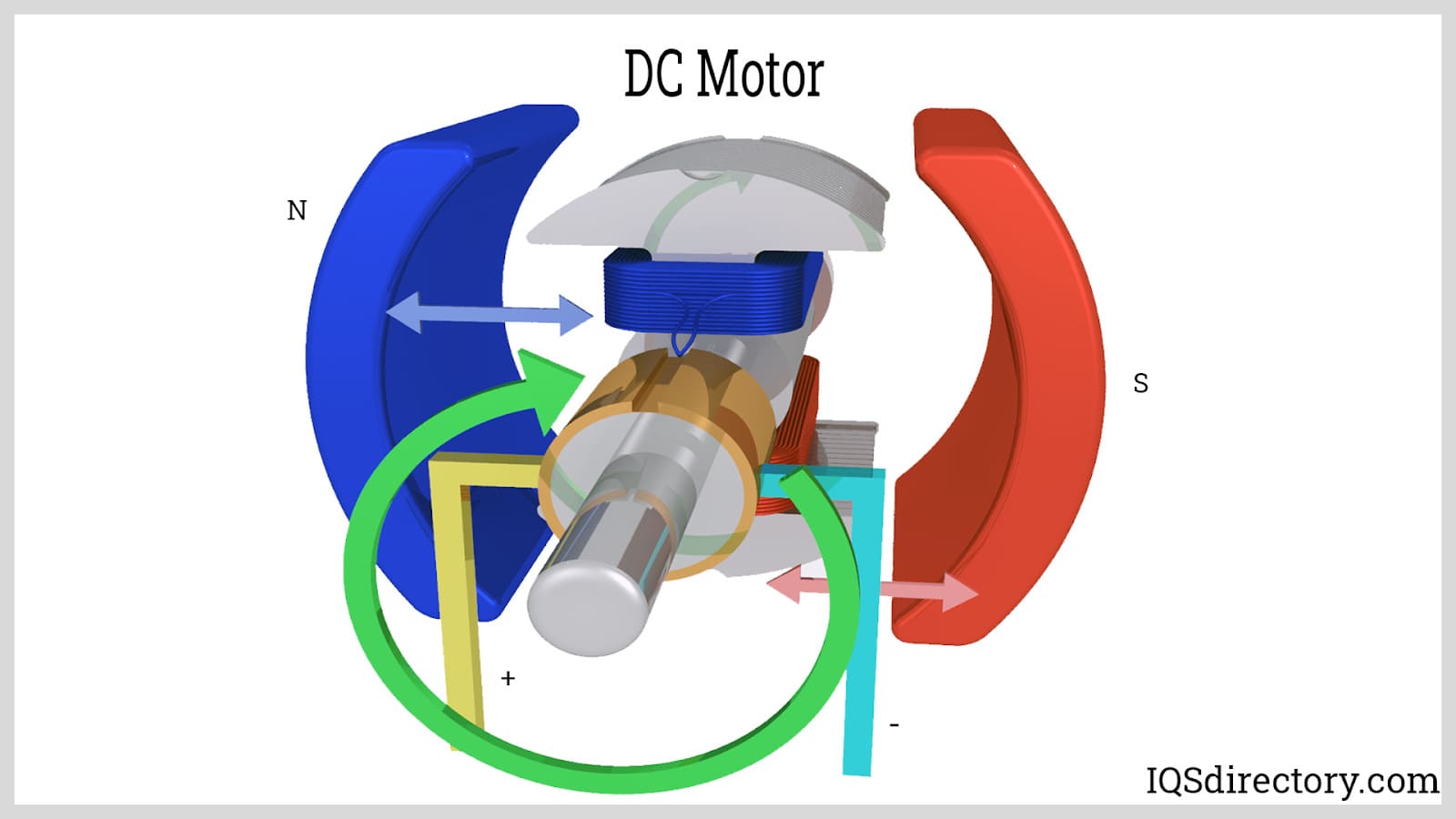
12V Motors
A 12V DC motor is inexpensive and small, but powerful enough to be utilized for various applications. One property of a 12V DC motor is its operating voltage. When a battery powers a DC motor, low operating voltage is generally preferred because fewer cells are needed to achieve the specified voltage. However, at high voltages, electronic devices to drive a motor are generally more efficient. Although functioning is possible with voltage as low as 1.5V which goes up to 100, the most usual are the 12V DC motor, 6V DC motor, and 24V DC motor. Other key characteristics of a 12V DC motor include the operating torque, speed, current, and power.
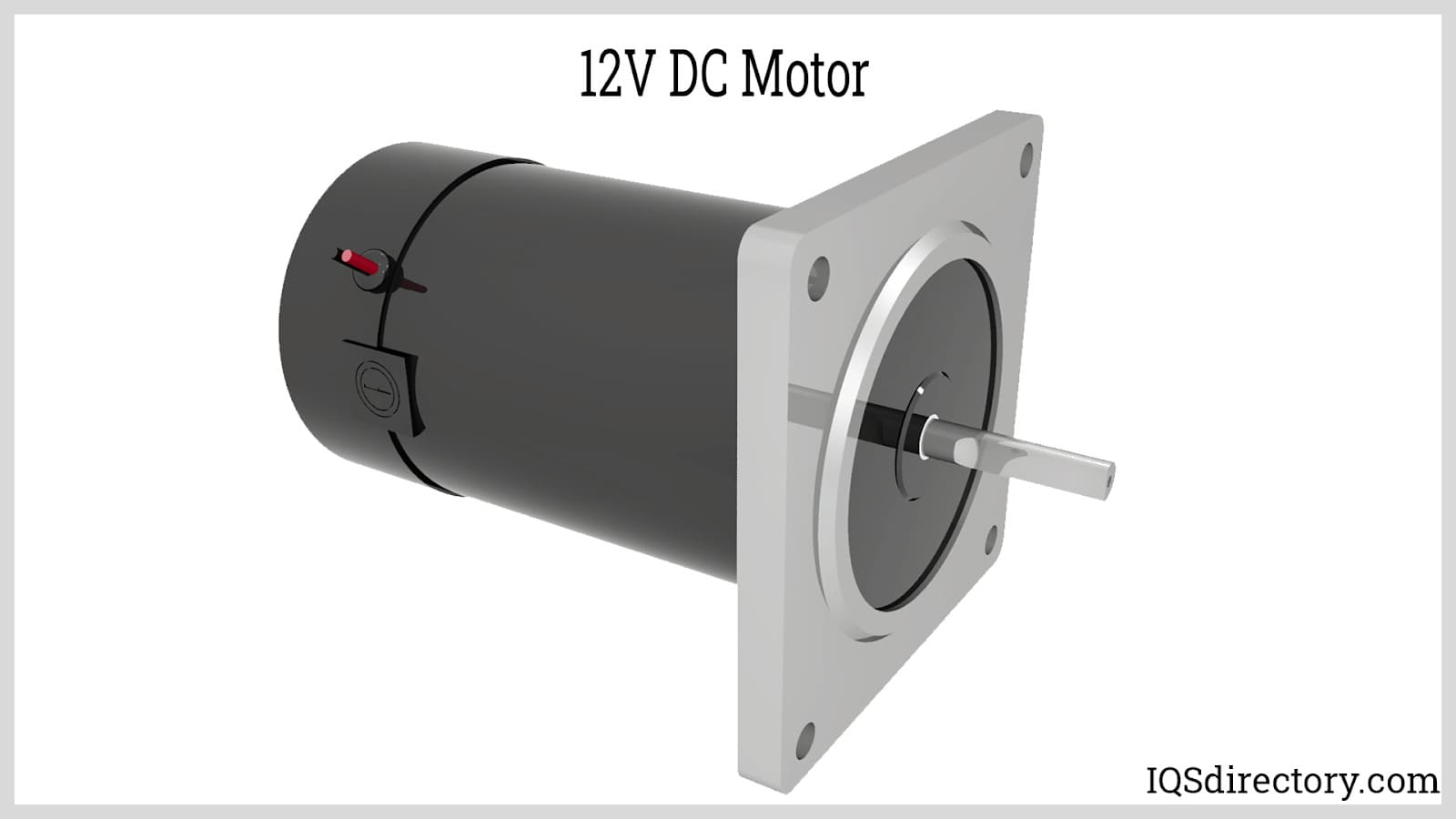
Most typically, 12V DC motors are brushless and are able to operate without the usage of brushes to move the electrical current. Whereas brushed motors can face possible problems due to their more complicated design. The design of the 12V DC brushless motor has eradicated most of these issues. The main parts of a 12V brushless DC motor are an external rotor permanent magnet, either a single coil or three coils. Accessories could be drive electronics and a type of sensor.
Instead of utilizing brushes to move electric current, 12V DC brushless motors move the current through a sensor, which is commonly known as a Hall Effect sensor. While 12V DC motors may also mean a type of AC motor, it is very uncommon in relation to the overwhelming status of 12V DC motors.
Brushless Motor
A brushless motor is a type of DC motor (BL motor or BLDC motor), also referred to as an electronic commutated motor (EC or ECM motor). It could also be called a synchronous DC motor. This is a motor utilizing direct current electric power. It utilizes an electronic controller to turn on DC currents to the windings creating a magnetic field that successfully rotates in space and the permanent magnet rotor rotates by following. The controller adjusts the amplitude and phase of the DC current pulse to control the torque and speed of the motor. This control mechanism is a substitute for the brushes or mechanical commutator utilized in numerous conventional electric motors.
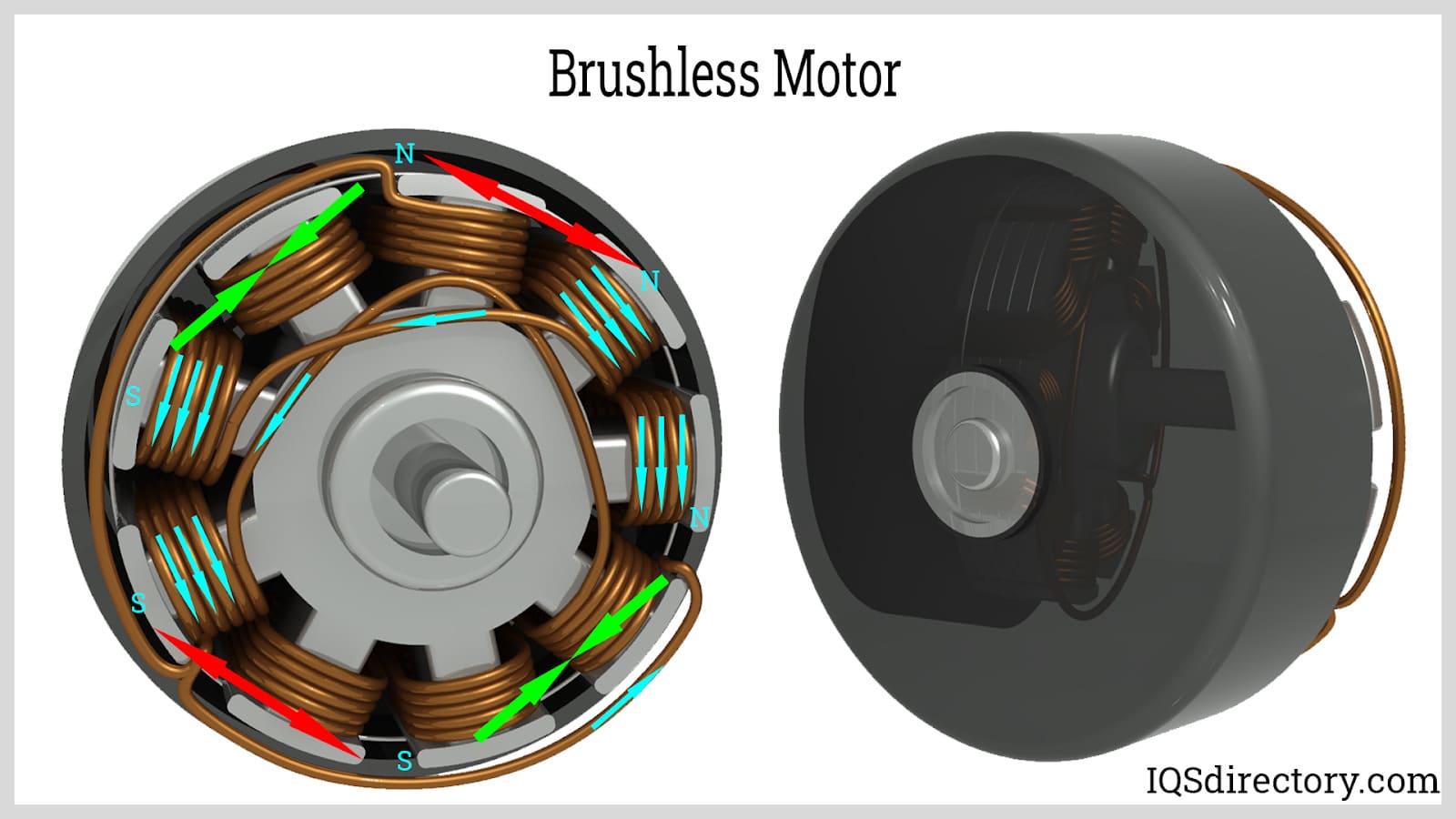
The manufacture of a brushless DC motor is generally similar to a permanent magnet DC motor, but may also be an asynchronous/induction motor, or switched reluctance motor. They may also utilize a neodymium magnet and be out-runners (the rotor surrounds the stator), in-runners (the stator surrounds the stator), or axial (the stator and rotor are parallel and flat).
The benefits of brushless motors over a brushed motor are high speed, high power-to-weight ratio, close to instantaneous torque and speed control (rpm), low maintenance, and high efficiency. Brushless motors find use in computer peripherals (printers, disk drives), portable power devices, and vehicles varying from automobiles to model aircraft. In current washing machines, brushless motors have enabled the replacement of gearboxes and rubber belts using a direct-drive design.
Stepper Motors
A stepper motor, also referred to as a stepping motor or step motor, is a brushless DC motor that divides a full revolution into a number of equivalent steps. The motor's position may be instructed to change and hold at one of the equal steps without using any positional sensor for feedback, as long as the motor is appropriately sized for the use in respect to speed and torque. Brushed DC motors continuously rotate when direct voltage is put on their terminals. A stepper motor is known for its characteristic of conversion of a chain of input pulses square waves to precisely defined increments in the shaft’s rotational point. Each pulse spins the shaft in a fixed angle.
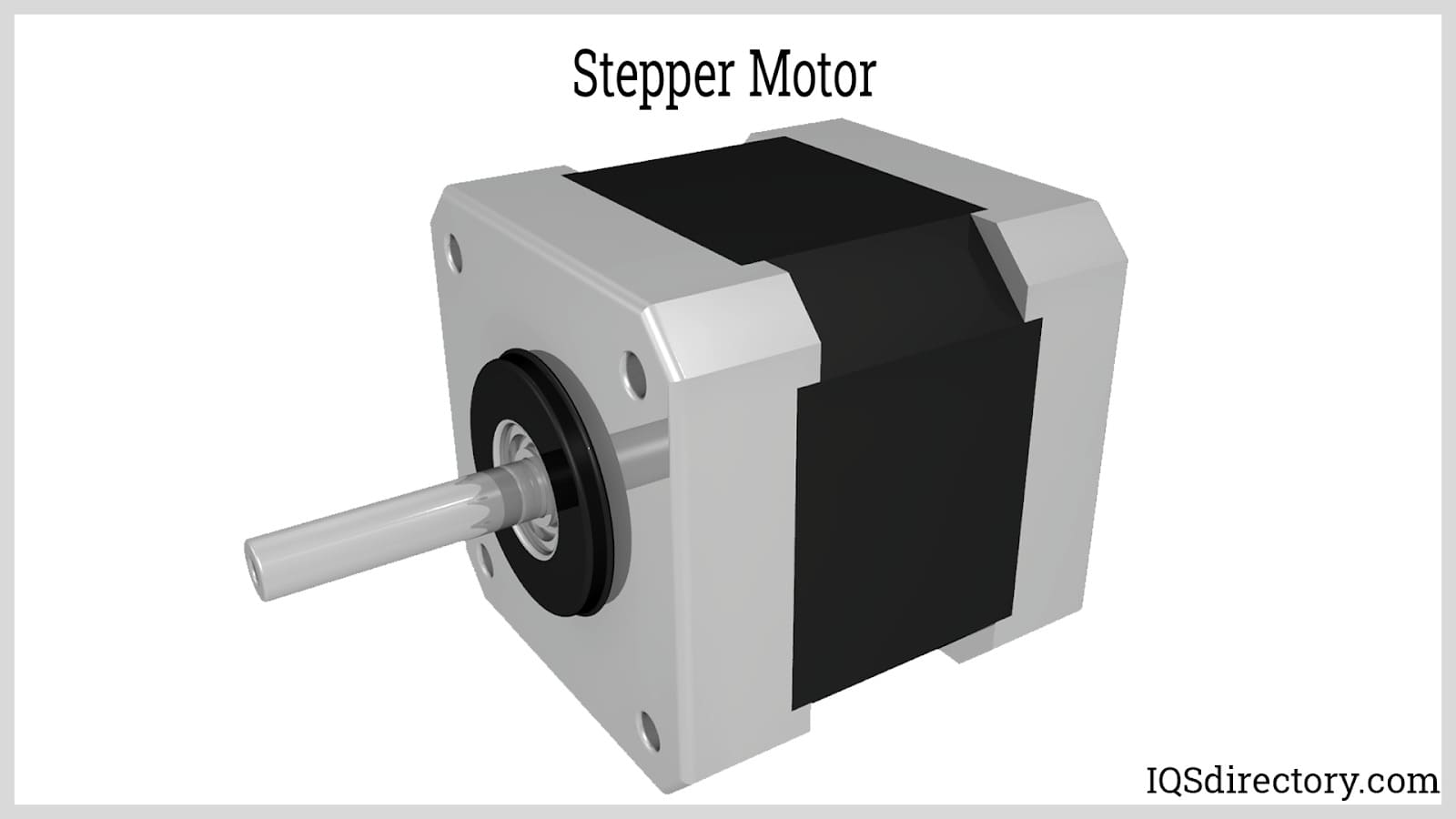
Stepper motors ultimately have numerous toothed electromagnets placed as a stator surrounding a central rotor, which is a gear-shaped iron piece. The electromagnets are powered by a microcontroller or an external driver circuit.
To make the shaft first rotate, one electromagnet is powered, which attracts the gear's teeth magnetically. When the teeth are aligned to the initial electromagnet, they are marginally offset from the following electromagnet. This means when the following electromagnet is switched on and the initial is switched off, the gear spins a little to align with the following one. From there the procedure is repeated. Each of those spins is called a "step," with an integer number of steps completing a full rotation. In that way, a motor may be turned using a precise angle.
AC Motors
An AC motor is an electric motor powered by an alternating current (AC). The AC motor generally comprises two primary parts: an outer stator with coils energized by an alternating current to create a spinning magnetic field. An inner rotor attached to the shaft creates a second spinning magnetic field. The rotor’s magnetic field could be created by reluctance saliency, permanent magnets, or AC or DC electrical windings.
Less popular, AC linear motors function on similar rules as rotating motors but they have their moving and stationary components laid out in a straight line set up, creating linear movement instead of rotation.
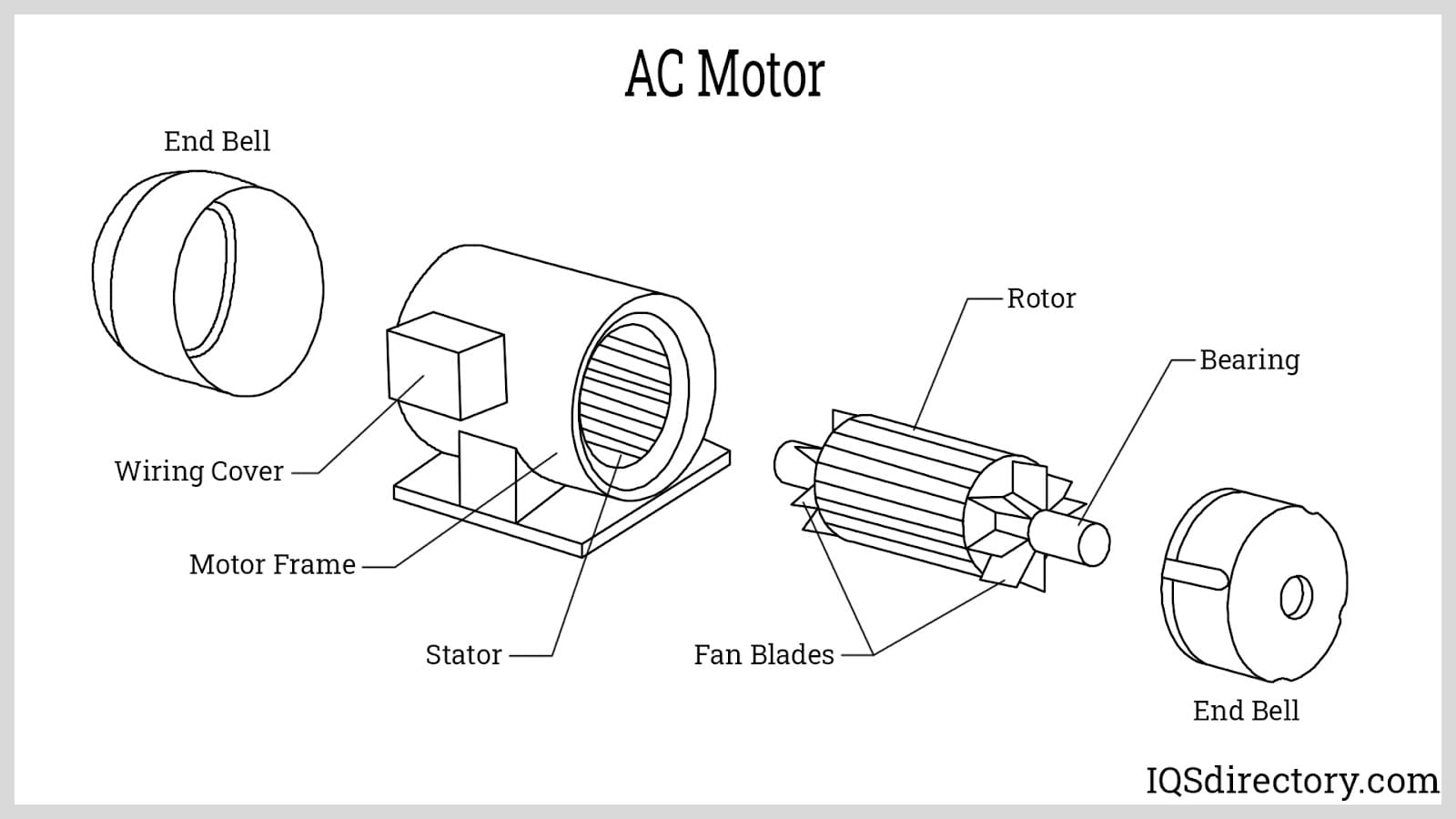
The two primary kinds of AC motors are synchronous motors and induction motors. The induction or asynchronous motor always depends on a small variance in speed between the rotor shaft speed and the stator spinning magnetic field called slip which induces rotor current in the AC winding of the rotor. Therefore, the induction motor can’t create torque close to synchronous speed where slip (induction) ceases to exist or is irrelevant. In comparison, a synchronous motor doesn’t depend on induction of slip for functioning and utilizes either salient poles (projecting magnetic poles), permanent magnets, or an individually excited rotor winding. The synchronous motor creates its ranked torque at accurately synchronous speed. The brushless wound-rotor double supplied synchronous motor mechanism has an individually excited rotor winding which does not depend on the rules of slip induced current. The brushless wound-rotor double supplied motor is a synchronous motor which can work exactly at the power source frequency. Other kinds of motors involve eddy current motors and DC and AC mechanically commutated machinery where speed relies on winding connection and voltage.
1HP Electric Motors
Horsepower or HP is a standard unit utilized to express the rate of mechanical energy expenditure. A power level of one HP is roughly equal to 746W or 0.746kW. While the horsepower, and the kilowatt, can all be reduced to similar dimensional units, the horsepower is hardly utilized to express power in any manner besides mechanical.
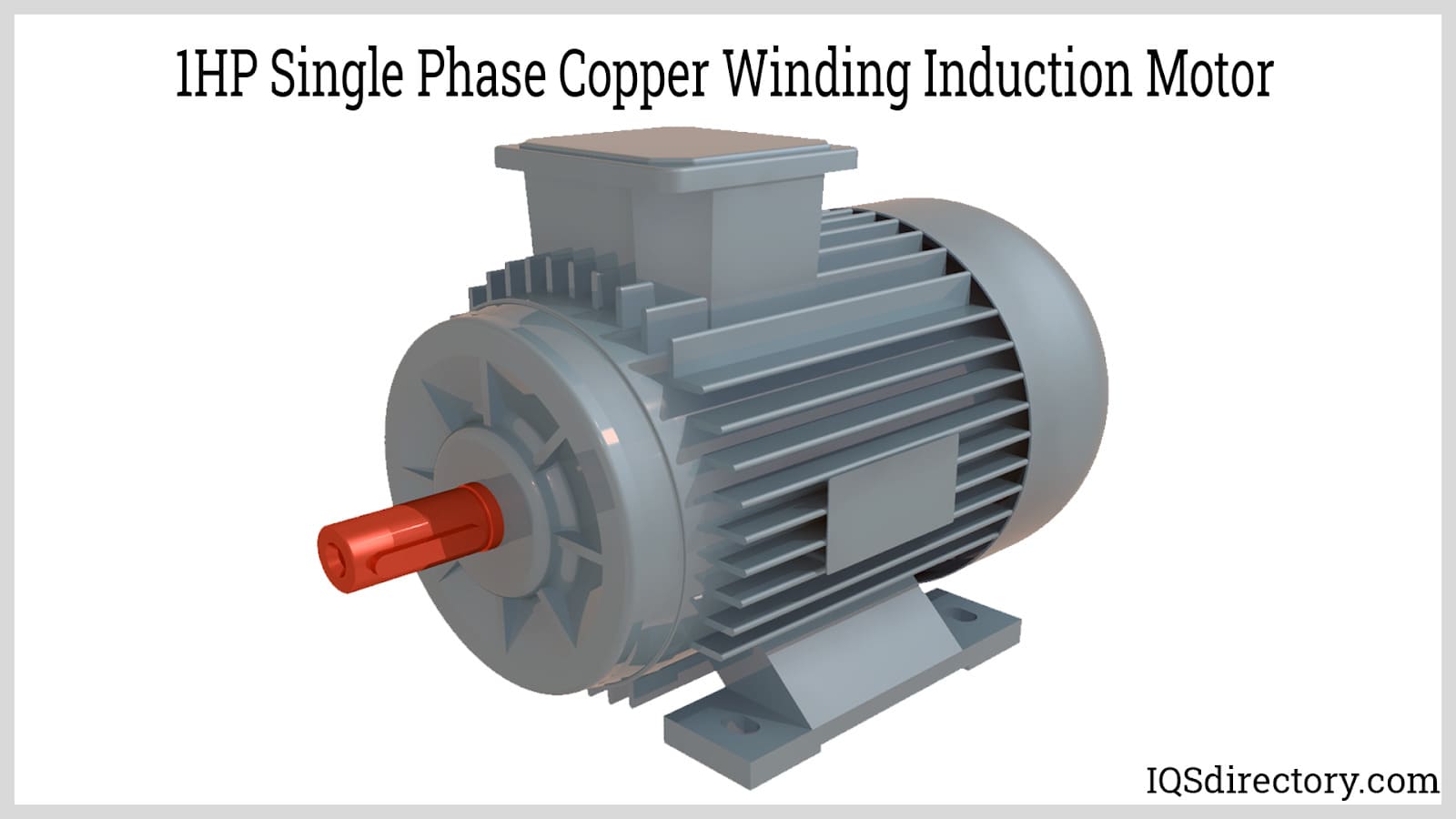
Nameplates on electrical motors display their output power, not the input power. This is power output at the shaft and not the power supplied to drive the motor). This output power is generally denoted in watts or kilowatts. In the United States of America, the output power is denoted in horsepower, which for this reason is defined as precisely 746 W. 1HP electric motors could be AC motors or DC motors. These types of motors are usually found in vehicles or electric boats.
2HP Electric Motors
Just like the 1HP electric motor, a 2HP electric motor works the same way by outputting power at its shaft. In kilowatts, this power is about 1.49kWIt could either be DC or AC type (Single phase or three phase). A 2HP electric motor is used to power boat propellers and industrial cooling fans or as an induction motor.
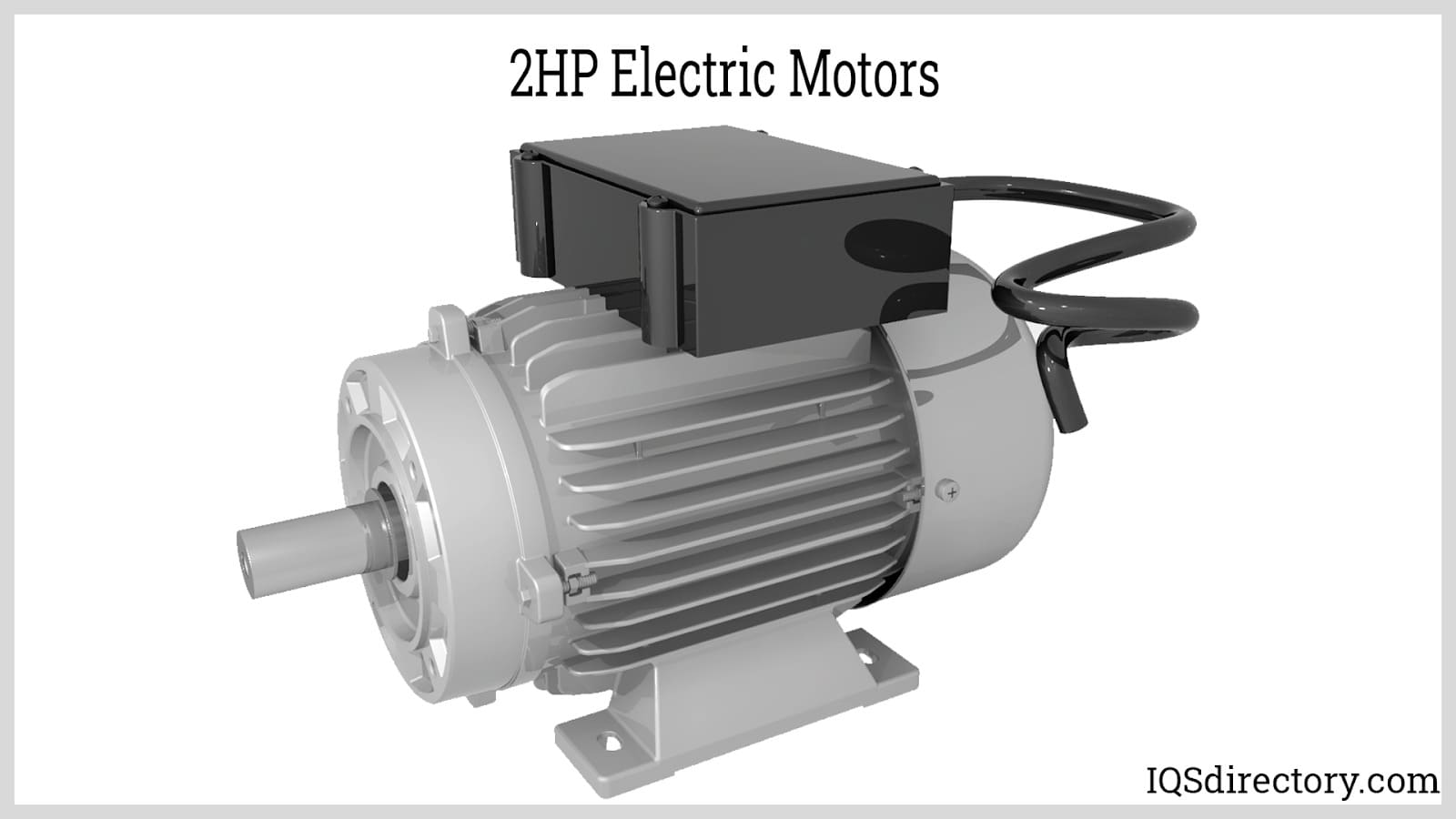
3 Phase Motors
Three-phase motors are an AC motor type which is an exact example of an induction motor, also called an asynchronous motor. The motors comprise three major components – the rotor, the stator, and the enclosure.
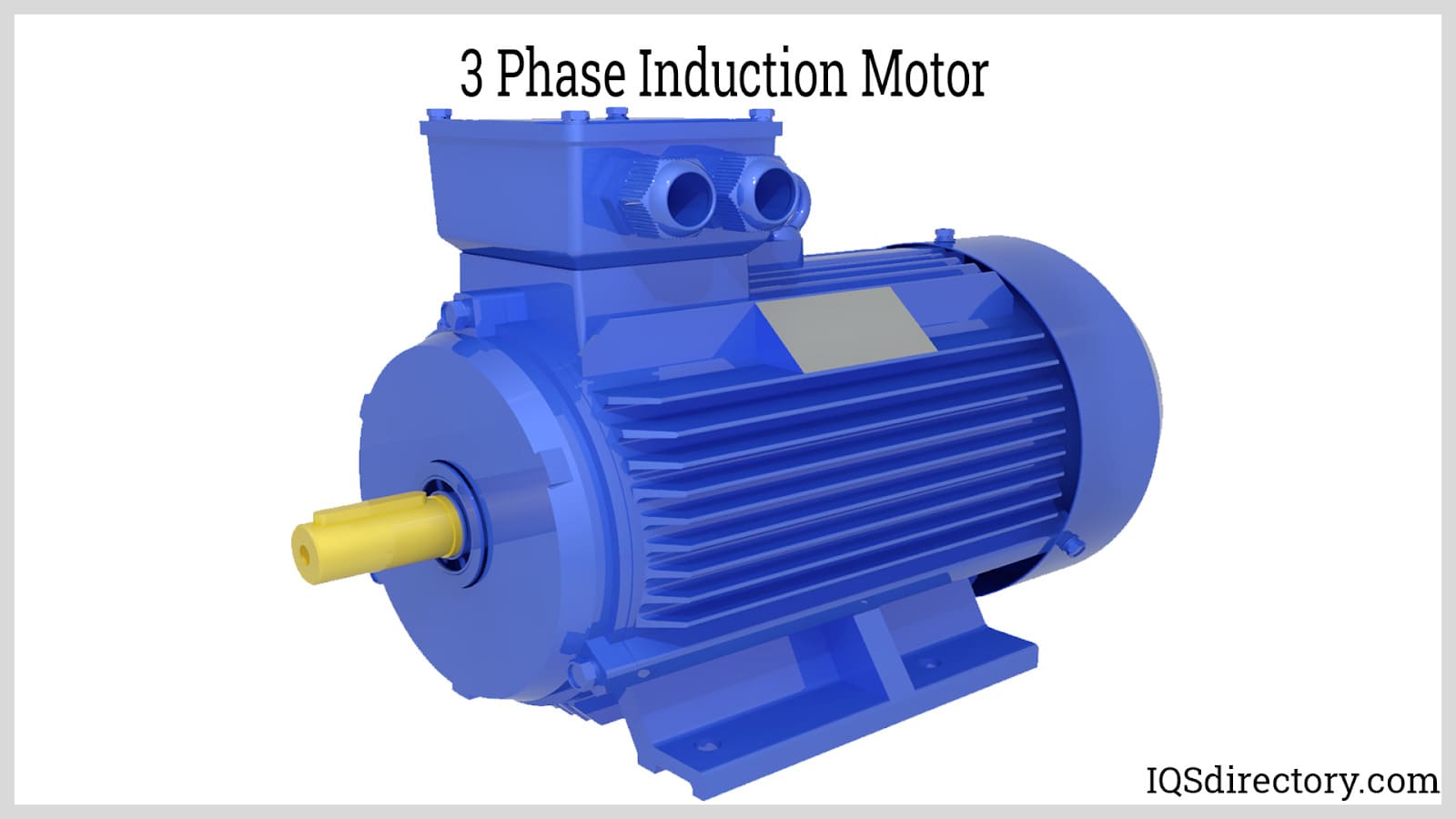
The stator comprises a sequence of steel alloy laminations that are wound with wires to make induction coils, one for each power source phase. Each stator coil is powered by a three-phase electric supply.
The rotor also comprises metal bars and induction coils connected to make a circuit. The rotor surrounds the motor shaft and it is the motor part which rotates to make output mechanical energy of the motor.
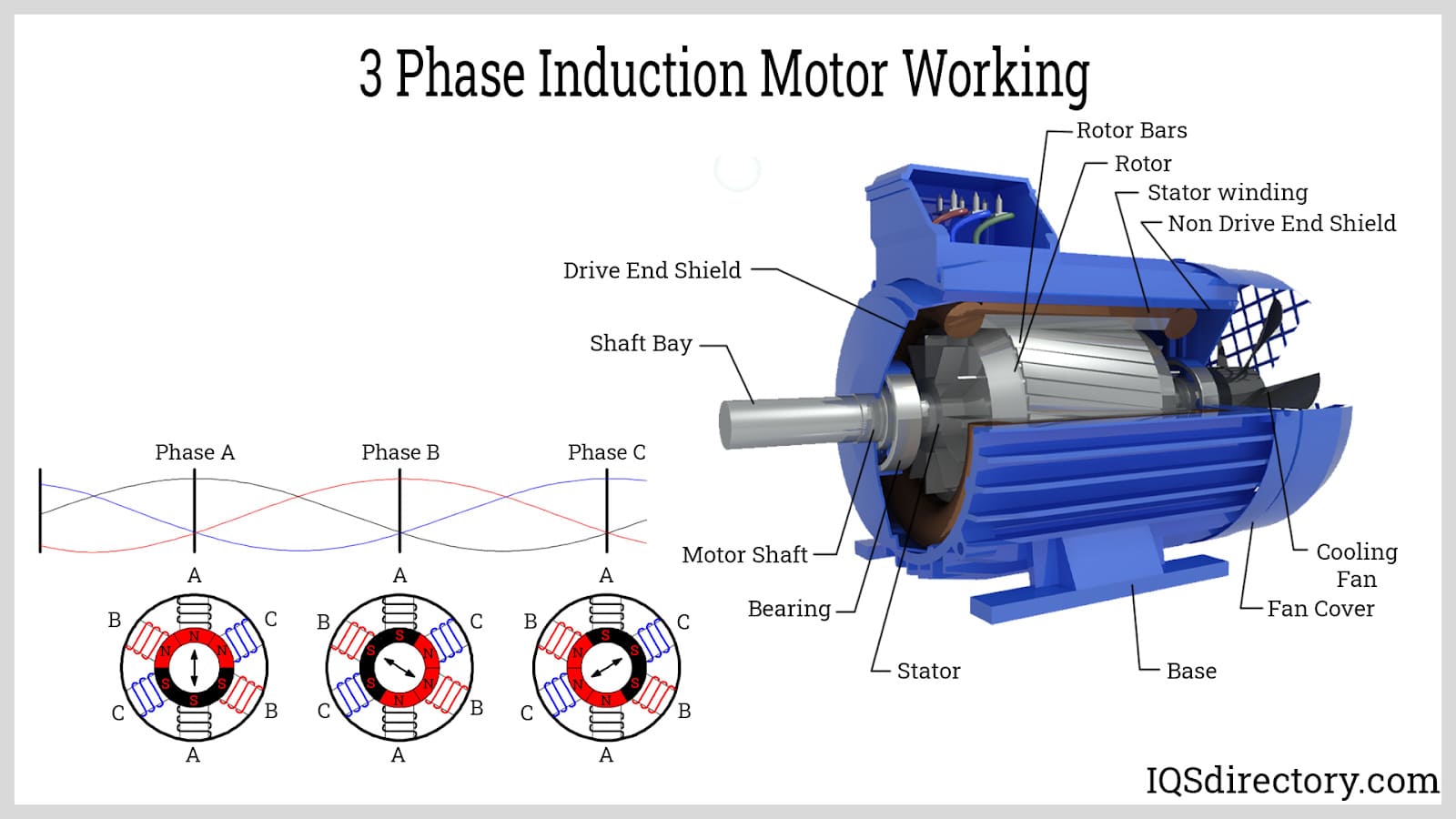
The casing of the motor keeps a rotor with its shaft on a collection of bearings to lower the friction of the revolving shaft. The casing has end caps which hold the bearing mountings and contain a fan which is attached to the shaft which rotates as the shaft turns. The rotating fan draws in ambient air from outside the casing and forces the air through the rotor and stator to cool the motor parts and dissipate heat which is created in the many coils from coil resistance. The casing also commonly has elevated mechanical fins on the outside, which further dissipates heat to the outer air. The end cap will also offer a place to contain the electrical networks for the three-phase source to the motor.
Single Phase Motors
A single phase motor is a rotary machine powered electrically which can convert electrical energy into mechanical energy. It works by utilizing a single phase power source. They have two types of wires: live and neutral. Their power can get up to 3kW and input voltage varies in unison. They only have one alternating voltage. The circuit functions with two wires and the AC current that flows across them is always constant. In many cases these motors are small with a small torque.
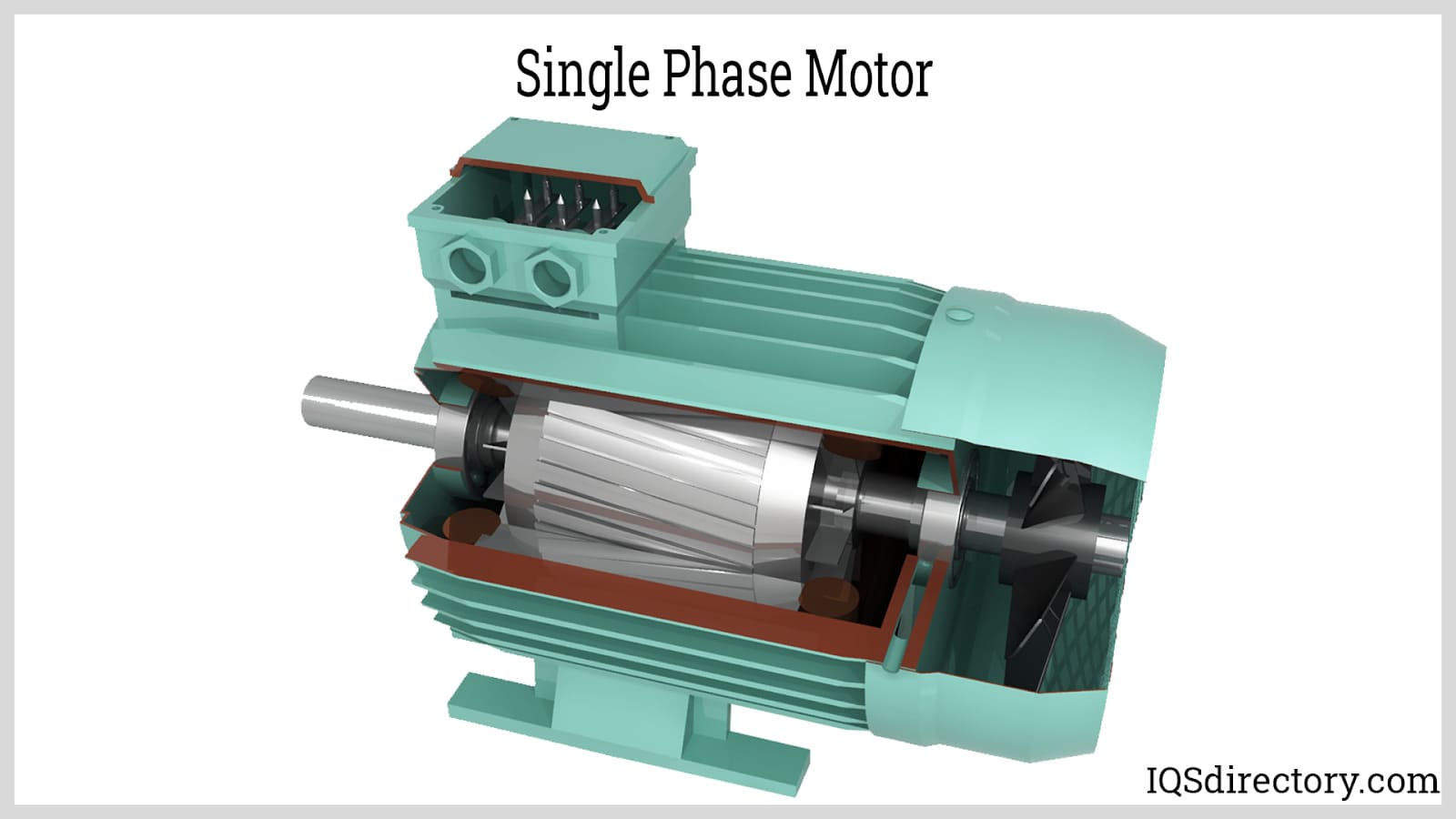
However, some single phase motors have a power of up to 10 HP which can operate with connections reaching up to 440V. They do not produce spinning magnetic fields, they can only produce an alternating field, which implies that for start-up they require a capacitor. They are simple to maintain and repair, as well as affordable. This type of motor is utilized mainly in offices, stores, homes, and non-industrial small companies. Their most popular uses include home and business HVAC, home appliances and other appliances like drills, air conditioning systems, and garage door closing and opening systems.
Industrial Motors
Industrial electric motors convert electrical power into mechanical power. Industrial motors produce either a rotary or linear force. Although there are types of industrial motors powered by DC current sources, they are very often energized by alternating current (AC) supplies like the power grid or generators.
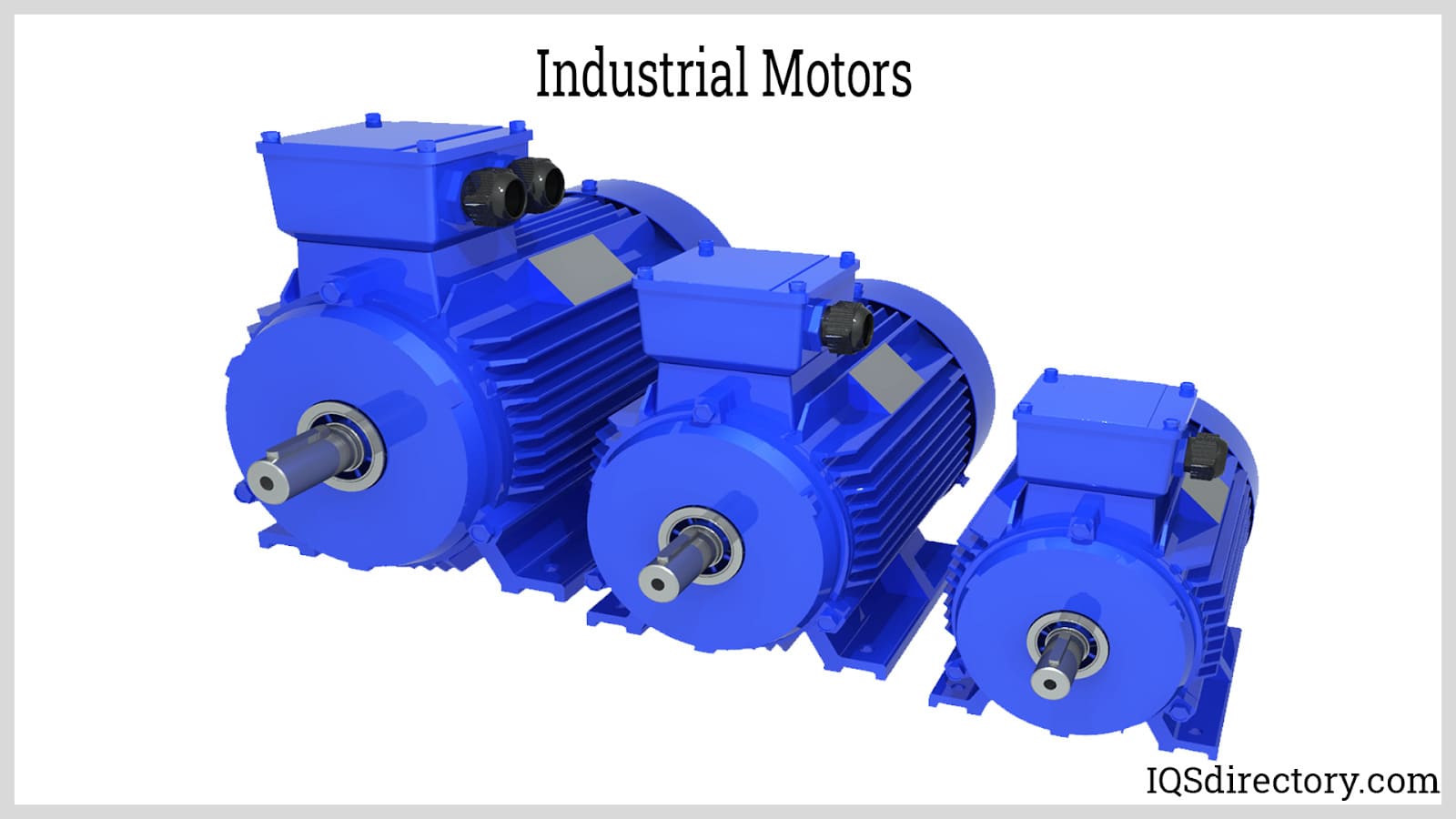
The main components of an industrial motor are the rotor (armature), stator, air gap, winding (coil), and commutator. Types of motors used in industrial motors include DC synchronous, AC synchronous, and AC induction (asynchronous) to name a few.
Servo Motors
A servomotor or servo motor is a linear actuator or rotary actuator which enables precise control of linear or angular position, acceleration, and velocity. It comprises an appropriate motor coupled with a sensor for feedback of position. It also needs a relatively complex controller, usually a dedicated device designed especially for usage with servomotors.
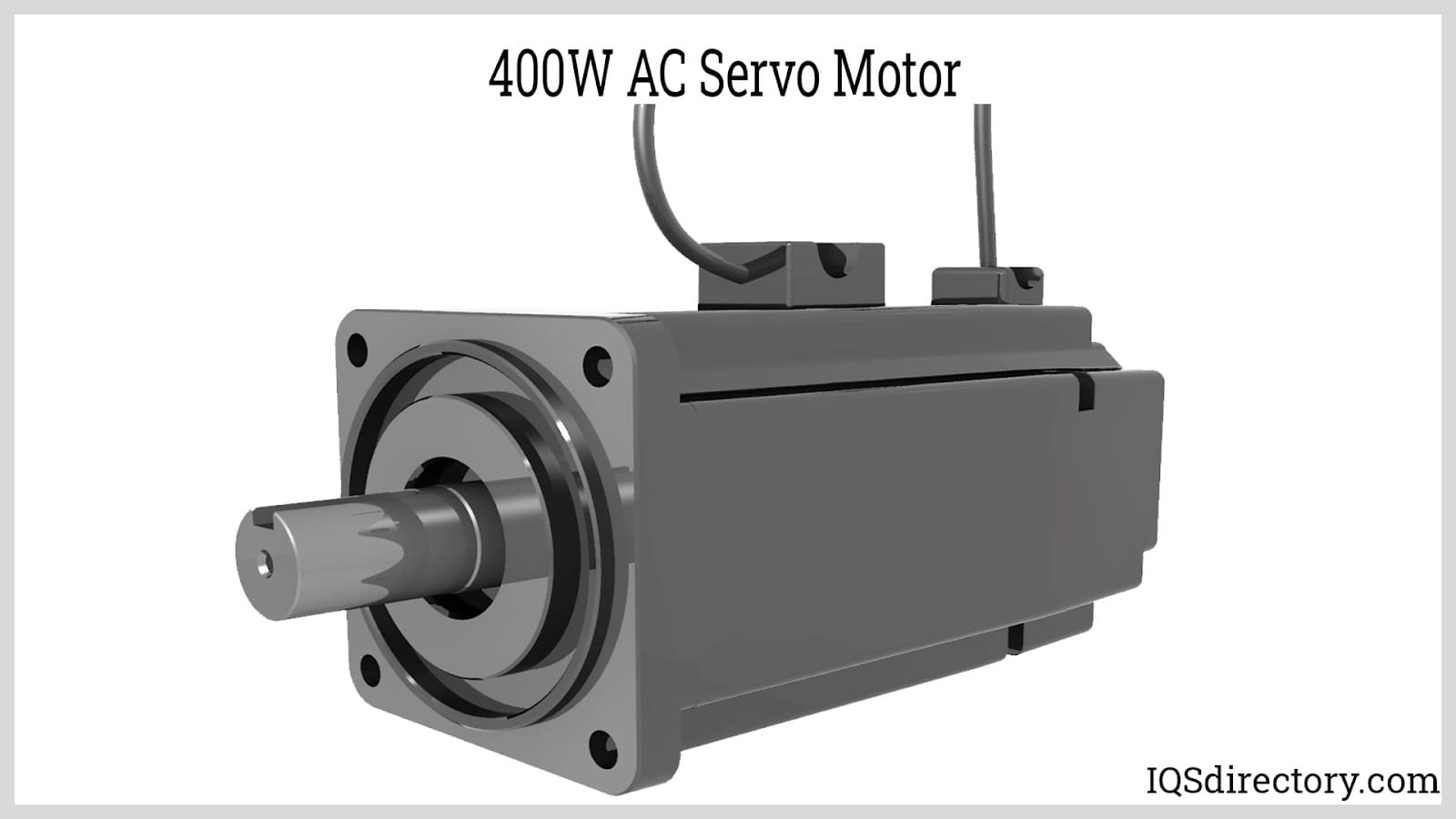
Servomotors aren’t an exact class of motors, though the name servomotor is often used to state a motor appropriate for usage in a closed-loop control system. Servomotors are utilized in applications like CNC machinery, robotics, and automated manufacturing.
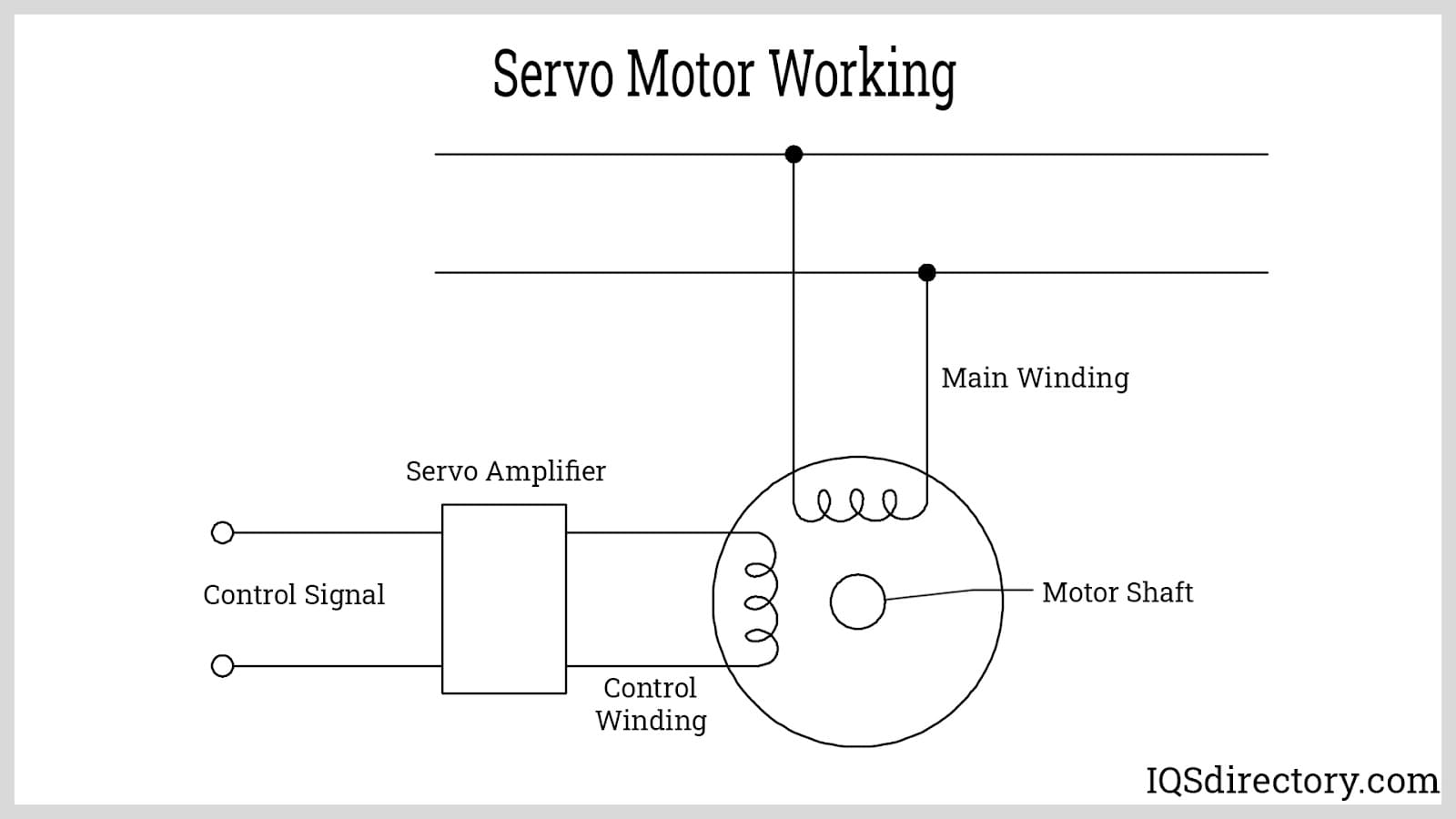
The type of motor used is not important to a servo motor and various types can be utilized. At the most basic, brushed DC motors (permanent magnet) are utilized, owing to their low cost and simplicity. Small industrial servo motors are generally brushless motors electronically commutated. For big industrial servo motors, AC induction motors are generally used, at times with variable frequency drives (VFD) to allow speed control. For ultimate performance in compact packages, brushless AC motors using permanent magnets are utilized, effectively big versions of brushless DC motors.
Chapter 3: Applications and Benefits of Electric Motors
This chapter will discuss the applications and benefits of an electric motor.
Applications of Electric Motors
The applications of electric motors primarily include fans, blowers, machine tools, turbines, pumps, power tools, compressors, alternators, rolling mills, movers, ships, and paper mills. The electric motor is an important device in various applications like high voltage AC heating, cooling & ventilating equipment, motor vehicles, and home appliances.
Benefits of Electric Motors
- The main cost of electric motors is less in contrast with fossil fuel engines, however the HP rating of both are alike.
- Electric motors have moving parts, hence the lifespan of electric motors is longer.
- The capacity of electric motors reaches 30,000 hours when maintained properly.
- Electric motors are very efficient and automatic control allows for automatic stop and start functions.
- Environmental friendly since they do not release pollutants.
Drawbacks of Electric Motors
- Big electric motors are difficult to move, and consideration must be done for the exact current and voltage supply.
- In other cases, costly line expansions are compulsory for isolated zones where electrical power is inaccessible.
- When utilizing a high HP motor and a low load factor, there may be a high expense per hour of working.
Safety Rules of Electric Motors
- Work area must always be kept well-lit and clean.
- All motors have many small components; young children must be kept away from the work area.
- Motors rotate very fast; PPE must always be worn.
- Motor must not be left unattended.
- If a battery is left shorted for long durations of time it might rupture or explode.
- Rated operating voltage must not be exceeded. High voltages might cause overheating and create fires.
- Motors must be operated by qualified personnel.
Electric Motor Maintenance
The maintenance of electric motors considers:
Cleaning and Maintenance Routine
Every company must have a cleaning schedule in place. Simply keeping a motor clean significantly improves lifespan and performance. A motor must never have excessive dust, grease, or other debris.
Motor Lubrication
It’s possible to over lubricate an electric motor, which may lead to internal issues. However, a motor needs lubrication to work at maximum performance level. Every electric motor needs a different amount of lubrication. Lubricating a motor very early or very late may lead to premature tear and wear. Also, manufacturers generally recommend specific lubricants designed for their electric motor.
Bearing Inspection
Motor bearings face most of the tear and wear, so it’s natural to expect issues from them from time to time. To prevent bearings from wearing out prematurely it must first be assured the motor is aligned appropriately. Misalignment may significantly stress the bearings. Also, improper lubricants cause bearings to wear out earlier than they must. One common sign a bearing becomes faulty is an overheating motor.
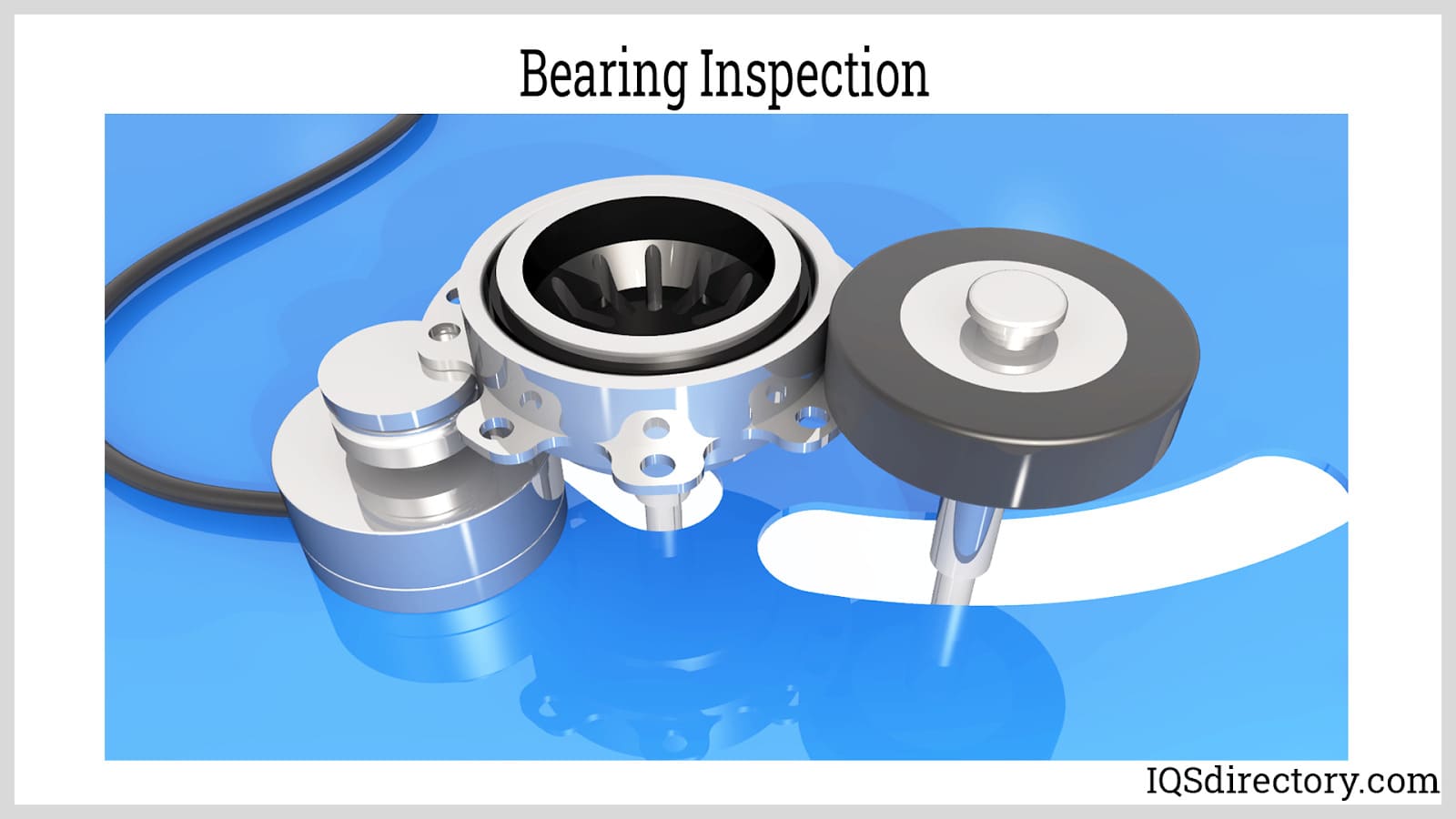
Reducing or Eliminating Vibrations
Every motor vibrates to some extent, but excess vibration may cause severe damage. The moment a motor vibrates more than normal, it must be turned off. The cause is usually a mechanical misalignment, a damaged bearing, or belt tension too high.
Rotor and Stator Inspection
The stator and rotor are the important parts of the motor. Any gaps around these parts must be measured and also with the diameter clearance. Clearance may differ depending on the electric motor and bearings.
Recording Findings
Longevity and wear and tear can’t be monitored if findings are not being recorded. Every time a motor is inspected and bearings must be replaced or the belt tension adjusted, and so on, note must be taken. In addition, when lubricant is added to the bearings or motor it must be documented. Upcoming maintenance and expenses can be better anticipated and planned accordingly.
Conclusion
Electric motors convert electrical energy to mechanical energy. Most of them work via the interaction of the motor magnetic field and electrical current in a wound wire to produce force in the manner of torque supplied on the motor shaft. The most important parts of a motor are the rotor and the stator. They may be energized by alternating or direct current. There are many types of electric motors including induction, servo, three phase, and industrial motors to name a few. They are used in electric vehicles, air conditioners, ships, and hydraulic machines.
Original source: https://www.iqsdirectory.com/articles/electric-motor.htm
- Tags: aliexpress electric bike, aliexpress Electric Car, aliexpress electric folding bike, aliexpress electric mountain bike, aliexpress electric scooter, aliexpress road electric bicycle, aliexpress self balancing scooter, aliexpress unicycle, Electric Bike Conversion Kit, Electric Scooter, Electric Skateboard, Electric unicycle, mobility scooter, personal transporter